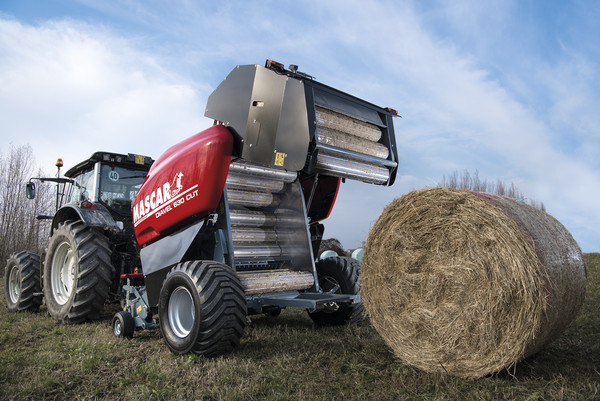
Fast and efficient, the new generation round balers
The best way to conserve forage and straw is to make sure the bale has been formed correctly. The category of balers in most widespread use are round balers, The two types of these balers are those with a fixed compression chamber and a variable chamber
The finest quality of hay forage, as well as straw, requires careful control of all the phases of harvesting, from mowing to baling. Baling allows a substantial reduction of the volume of forage by compressing it while paying attention to the characteristic of the product – type of forage and straw, humidity, type of feed and the like – as well as the parameters for regulating the bale maker, the type of baler, density of the product, type of binding, etc.
It is well known that especially in northern Italy haymaking is performed in a time of year when the weather is changeable, mainly during the first mowing of the season. This meant that these operations must be timely to ensure big yields for the machine. Round and big balers have for some time replaced traditional square balers and are now used in the attempt to achieve these results.
Construction features
Though there are various differences in various types of balers, they can be classified in two large groups based on the baling chamber; round balers which produce cylinder-shaped bales with fairly large diameters, rectangular balers which at times include gigantic big-baler models and the traditional square balers. These latter types are always trailed by the tractor PTO and powered by a flywheel with a mass of dozens kilometers for the traditional machines and hundreds of big-balers and a sturdy piston in the forming chamber of the rectantular baler. The strong inertia of the flywheel handles the load peaks of the piston to compress the forage feed into the chamber by feeder rakes. The piston moves in a linear way with a frequency of about 30 to 80 impacts/min and is directly connected to a bulkhead in tempered steel which sections the product on entry and closes the forming chamber for the creation of bales in successive segments. The level of forage compression is regulated by controls which change the size of the bale discharge chute. When the bale has reached the proper length, set mechanically or electronically, the bale is bound by twine knotted by the twine holder. As the bale is formed twine is pulled from the twine box around the bale, a measuring wheel trips the tying mechanism and the needed with the help of a tucker finger to bring the second strand of tine through the knife arm guide, across the bill hook and into the twine disk. When the twine holder has secured both strands of twine in the disk, the bill hook starts its revolution which at ¾ the finger opens to complete the knot.
Collection of the forage from the field is done by the pickup mounted on the front of the frame built with a spiral rotor equipped with spring steel tines which rake up the product and conveys it to the feeding system and then on to the compression chamber. For the size of the chamber, usually 36 cm high and 46 cm wide, two knotters are almost always sufficient (whereas big-balers normally require up to six). The bale is removed simply by following the bale formed in the chamber which pushes it to the discharge chute.
The operations of the baler can be regulated, either mechanically on basic models or hydraulically on more sophisticated models, for the height of the pickup off the ground, for configuring the machine for road transport and for the level of bale compression and length.
In light of their work capacity, and power requirement, and costs substantially lower than those of big-balers, the category of round balers is now a popular category. There are two types, differentiated by their their bale forming chambers, fixed or variable, creating softcore or hardcore bales.
After the forage windrow has been picked up the product is sent to the baling chamber which, as it fills up with an outer wrap, begins compressing the round bale from the core outward. Then bale then goes to the binding process which can be with twine or net or plastic film wrap.
The variable round baler chamber uses a series of belts or rotating chains with tension controlled by rubber coated rollers powered by hydraulic cylinders. As the forage enters the chamber, the chains or belts move out from the center of the chamber to expand its volume and maintain the density of the product packed more or less constant. Moreover, with this method the final diameter of the bale can be varied within certain limits.
The fixed chamber of a round baler is also based on belts, chains or rollers which, however, rotate in a fixed location. The forage is wrapped around itself and pressure on the product beging only when the chamber fills. The core of these bales is generally less compact.
For both types, binding with twine or net, is done with the machine stopped with no producting arriving. The bale is rotated in the chamber and bound with twine or wrapped in net beginning on the exterior curve of the bale. Finally, the tailgate is opened and the bale drops to the ground.
Thanks to modern technology, the time and speed for operations of round balers has been substantially increased, even up to 15 km/h. In this case, the time needed for binding and dropping the bale is significant. To overcome this downtime, some manufacturers have recently presented models capable of solving this problem.