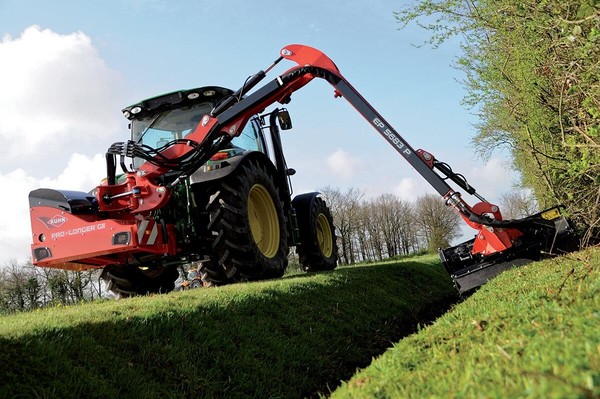
Brush cutter, a multipurpose equipment
By taking advantage of the hydraulic power transmission, brush cutters can work with a considerable outreach compared to the tractors with which they are coupled. It is important to carefully take care of the maintenance of the cutting rotor and follow the procedures that guarantee safety during the execution of the work
Brush cutters are basically used to shred both herbaceous and woody plant material of limited size (e.g. grass, small shrubs, and branches), and can also work at considerable distances from the tractor to which they are coupled. They are typically multi-purpose machinery, suitable for the maintenance of ditches and canals, road edges, headlands, the branches of some trees, etc.
The working head, with a hydraulic handling system, is very similar to that of the common shredder: the main difference is that, unlike the latter, the brushcutter booms can work with a significant overhang compared to that of the tractor, this is why they seldom have widths of work over 2 meters. Therefore, logically, the main technical-operational characteristics of this equipment are the outreach (i.e. the distance of the working part from the tractor), the width of its working front, the possible inclination and the mass.
Like the common shredders, the working organ is a horizontal rotor on whose external development the tools are arranged, followers hinged on pins, which can be knives or hammers of various shapes and sizes. The mass and size of the single tool are selected according to the material to be shredded (prunings, grass, shrubs, twigs, etc.). The tools' freedom of movement is of vital importance during rotation to effectively absorb shocks with particularly leathery materials, and when there are foreign bodies such as stones, small stumps, etc.
A further difference to note is the handling mode of the working organ: in the shredders, the motion is transmitted mechanically through the power take-off of the tractor (with undoubted advantages for the transmission efficiency), while in the brushcutter arms a hydraulic engine is necessarily adopted, since the mechanical solution would be complex (therefore expensive) and inevitably heavy, with an unsustainable burden for a machinery that needs to work with a considerable reach.
Therefore, in this case, the use of high-strength steels and sections increasing the rigidity of the various components becomes vital, since, inevitably, the cantilevered mass brings to a destabilizing moment, very critical in terms of the tractor safety.
The French brand Rosseau offers an interesting alternative, a range of E-TP brush cutters, consisting of models in which the shredder, instead of being hydraulically operated, is electrically started. Practically, the PTO of the tractor operates an electric generator which, through a cable of adequate size, powers a 33-kW brushless electric engine connected to the rotor, which rotates at a variable speed between 500 and 3000 rpm. However, the three models making up the range (E-Kastor, E-Thenor and E-Fulgor) maintain the classic hydraulic drive to orientate the head and the movement of the arm elements. Although this is a technically interesting solution, at the moment the cost of this equipment is significantly higher than most of the Italian production which, even in this sector, is an excellent example of the excellence that distinguishes the national manufacturers. As many as 90% of the brush cutters produced in Italy are profitably exported.
The transmission of the movement
To mitigate the criticality of the cantilever mass, it is customary to connect the brushcutter arms to well-sized tractors, which are almost always also massively ballasted, precisely to increase the stability of the tractor-operator site. Therefore, although the power requirement of the working part is not particularly high (compared to the available power of the coupled tractors), it is logically important that the operator's independent hydraulic system is adequately sized to dispose of the heat inevitably generated, especially in the case in which it is necessary to operate for a long time in torrid climates and on leathery materials. Usually, in fact, on the brush cutter, the power transmitted mechanically through the PTO and the cardan shaft drives a hydraulic pump that takes the oil from a special tank, to send it under pressure through the distributors to the hydraulic cylinders for the movement of the arms and the hydraulic engine for the rotation of the working organ.
Connection methods
The brush cutters are almost always connected to the tractor through the 3-point linkage of the lift. Exceptions are the models with a very high reach, for which a fixed stirrup, in the side-ventral position is preferred.
To rebalance the highly destabilizing moment that inevitably occurs, normally there are counterbalancing masses suitably positioned on the opposite side, starting from the hydraulic oil tank. In any case, these are rather complex equipment to be installed and connected to the tractor, therefore, they remain always coupled to the tractor that carries them.
Safety
First of all, the controls for operating the moving parts must be hold-to-run, i.e. they automatically return to the initial position after release. They must be reached easily and without risks by the operator, but at the same time, their location must be such as to prevent accidental and improper activation by unauthorized persons. The possibility of stopping the working parts (rotating or oscillating) must also be guaranteed even while the power source remains active, preventing them from being accidentally restarted. It goes without saying that the safety of the brush cutters must necessarily also include regular, ordinary and extraordinary maintenance. The first includes the frequent routine operations of lube, cleaning and visual inspection, first of all, to control the extent of the "easing" that inevitably occurs because of the wear and tear in the various joints, that is, on the pins and bushings. This is as simple and quick as it is important because, in addition to reducing the precision of the work carried out, excessive loosening can, without a doubt, cause further destabilization of the tractor.
The periodicity of extraordinary maintenance depends, as expected, on the frequency and intensity of the work performed: the elements most involved in terms of replacement are all the parts naturally subject to wear (cutting tools, slides, sealing rings of the hydraulic cylinders, etc.) and hydraulic oil.
Tool damage, wear, and replacement
If it is necessary to change the tools of the cutting rotor, both to replace the worn ones, and to assemble different ones, more suitable for the work to be carried out (knives, hoes, heavy hoes, toothed hoes, hammers) it must be done very carefully, since it is a very critical intervention in terms of safety. The hinged tools rotate at hundreds of revolutions per minute and are subject to a remarkable centrifugal force: if they are not perfectly fixed, their detachment transforms them into actual bullets, capable of traveling many tens of meters at extremely high speeds, thus constituting a potentially lethal danger.
It must also be considered that uneven wear and / or accidental damage to some tools inevitably causes an imbalance of the rotor, causing increased vibrations which accelerate the wear of the bearings and joints which, in addition to decreasing the cutting efficiency, increase in this way, the work effort and consequently the consumption of diesel fuel ultimately reduce the quality and productivity of the work. If the replacement of the tools is selective, it is important to ensure that the mass of each new element is identical to the original ones, while also replacing the screws and fixing nuts, scrupulously respecting the directions possibly written in the use and maintenance booklet.