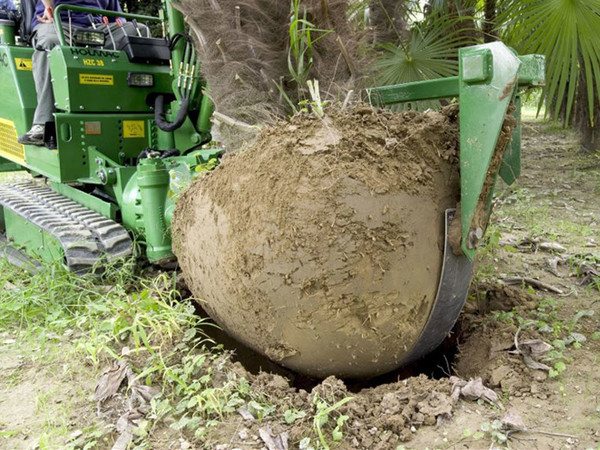
Tree diggers ensure good rooting
The digging up of tree species must be carried out with a root-ball of a size appropriate to the stage of development of the plant. The newest tree diggers respond well to the needs of this delicate operation
The nursery activity in Italy has always been traditionally very widespread. The planting of plants, as well as all the previous and following phases, are crucial to preserving their rooting and the following growth. Plant and sod digging, that is to say, the controlled digging-up is a crucial step to which the utmost attention must be paid. It is undoubtedly a massive operation for the workers if carried out manually. Its mechanization solves many problems: tree diggers, as well as the grubber-transplanting machinery, respond to this need. In detail, the formers are purely used in nurseries for the purpose of planting trees with the relative clod of earth, while the latter also carry out the planting.
In particular, with tree diggers, it is possible to intervene also on plants of considerable dimensions, carrying out every single uprooting in a few tens of minutes, with the intervention of no more than one or two operators. This allows for a significant reduction in working time, resulting in a significant increase in productivity.
Tree diggers components
This equipment is carried in front of a self-propelled machine (a tractor, a small excavator, a telescopic handler, etc.), which are also available in self-propelled versions in the most performing versions, using hydraulically operated movements.
From an operational point of view, the tree digger identifies a well-defined operation, but it can be carried out in two different ways as far as uprooting is concerned, that is to say, employing working parts with linear movements or vibrating. In the first case, the grubbing is more delicate, and it is indicated for some delicate species, while in the second case, it helps the penetration of the working organ in the soil, easing the detachment of the root apparatus of the plant.
The models working without vibrations are made up of 2-4 hydraulically operated spades that plunge more or less vertically into the ground in sequence, while later, some spears of different conformation cut the lower part of the clod in an arc and eradicate it. In smaller machines, spades are pushed down by hydraulic cylinders powered by the hydraulic system of the tractor to which they are coupled, while larger models, often self-propelled, are entirely independent. The resulting root-ball has, therefore, a truncated cone shape.
The vibrating blade tree diggers carry out the uprooting in a single solution: In this case, the working organ, made of high-strength steel and curved in shape, plunges into the ground along a curved trajectory, creating a root-ball shaped like a spherical cap.
Alternate sets of spades can be mounted on the linear motion tree diggers, so as to obtain different sizes of the clods, with increases in diameter of 5-7 cm. Furthermore, it is also possible to modify the depth of the root-ball, always of a few centimeters.
The truncated cone and hemispherical conformations of the clods that are obtained well suit the typical shape of the pots where the uprooted plants are located, so as to ensure the best stability in the handling of the material in the phases following the uprooting.
What the market has to offer
Models are available that make clods with a diameter from about 30 cm up to more than 1.5 m. The Extir-Plants B900 model, the most performing model, produced by Mac Bert from Ferrara, can make both truncated cone and spherical dome clods. In the first case, the maximum diameter is 90 cm, and 4 spades (which make the vertical cut) and 2 lateral spears cutting the taproot of the plant in-depth like with scissors. Conversely, only the lateral spears can be made to plunge into the ground 3-4 times, turning around the trunk of the plant. In this way, the obtained clod can reach as much as 1,8 m of diameter. This model, which has a considerable unladen mass of 1300 kg, must be coupled to a means capable of adequately powering the hydraulic system (which works at pressures up to 150 bar) and, at the same time, ensuring sufficient stability in the matching. Therefore, the manufacturer recommends matching with tractors with at least 70 Hp, better if they are well-calibrated. The models with higher working capacity are self-propelled, and use diesel engines with relatively low power ratings, from 20 to 40-50 Hp. The typical maximum forward speed of the vehicle is deficient, generally not exceeding 8 km/h.
Pazzaglia from Pistoia shows in its catalog a range of self-propelled models, based on tractors with rubber tracks placed in front of the device with vibrating curved blade, with a diameter from 18 cm up to 1.3 meters. The ergonomics level, as well as and the operator safety are high: Holmac from Padua offers models equipped with joystick controls placed with rationality and characterized by easy visibility for maneuverability without uncertainties. The profile of the chassis accompanying the cockpit is rounded and with elusive lines, so as not to hook the branches of the plants, thus reducing the risk of damage.
Accessories
There are several additional options for the tree diggers, including: the unusually wide adjustment of the blade holder arm, which makes it possible to install cutting elements of quite different sizes, from 25 cm to about 1 m. a device for lifting the clod above ground, for effective support of the plant and the clod after uprooting; the transversal inclination of the vibrating blade unit of 35° on both sides, to facilitate easy maneuverability even in confined spaces; a hydraulic system dedicated to the movement of the self-propelled machine, to increase its speed when getting closer to the plant; on the vibrating blade models, the mechanical isolation of the driver’s seat, for reduced operator stress.