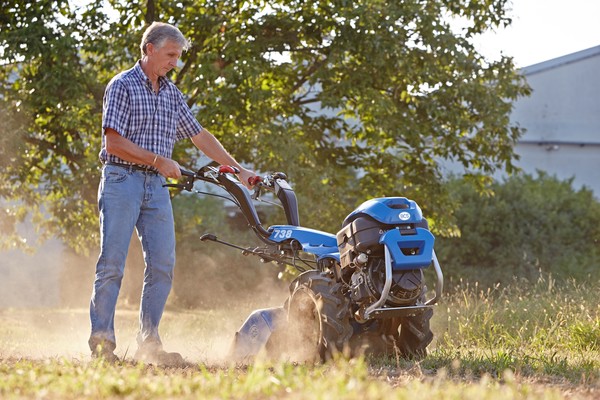
The small-scale mechanization of specialized crops
Many Italian farms are limited in size, and purchasing a conventional tractor is uneconomical or even impossible. For these realities, the ideal is to equip themselves with motor hoes and walking tractors, which, thanks to their small size and versatility, prove to be valuable aids in the production process
A fairly recent agricultural census noted that as many as 1.4 million machines, including walking tractors, motor hoes and motor mowers, were operating on Italian farms. This is undoubtedly an approximate number by default since it is well known that only machines intended for professional use are recorded in censuses, while those in the possession of hobbyists (in this case, numerous) are not included. It is easy to understand how tillers and cultivators are still extremely common means both among those who carry out highly specialized professional agricultural activities (heroic viticulture, nursery farms, floriculture, horticulture, etc.) and in farms that cultivate limited areas of land for which the purchase and use of a tractor is impractical or convenient.
It is worth mentioning that agricultural mechanization in Europe did not initially develop with the appearance of tractors but rather with these small single-axle machines equipped with a low-powered endothermic engine and driven by hand by an accompanying operator. The first examples of machines that can be likened to motor cultivators date back to the second decade of the last century, thanks to a Swiss manufacturer, Karl de Meyenburg, who devised a small two-wheeled vehicle equipped with a kind of tiller to break up the soil. In Italy, the first models of motor cultivators appeared around the same time, but it was in the 1950s that they experienced a true "golden age," thanks to companies that, having concluded the war effort related to World War II, needed to reconvert their production to civilian uses. These included Aermacchi, Moto Guzzi, Aeronautica Caproni, and Piaggio, but it was with the small artisans that walking tractors and power tillers became firmly established in the market. Some brands are still in operation today, such as Nibbi, Pasquali, Goldoni, Ferrari, BCS, Bertolini and others, while many others have ceased production after only a few years of operation. In most cases, these small manufacturers purchased engines from other companies specializing in the construction of diesel or gasoline engines, including ACME, Ruggerini, Lombardini, Slanzi, Guidetti, and VM, which have now disappeared or been absorbed into new companies.
Power tiller. This is a light, compact machine designed primarily for secondary tillage, such as seedbed preparation or weeding. Without propulsion organs (wheels or tracks), it is equipped with an engine, usually endothermic (powered by gasoline or diesel) or electric in the lighter versions, that drives a horizontal-axis rotor, usually no more than one meter wide, to which small curved, crescent-shaped or straight-toothed hoes are firmly attached. Set in rotation by mechanical transmissions, the hoes simultaneously allow the machine to move forward and till the soil; the latter is crushed and broken up to depths varying between 10 and 20 cm, depending on the model and possible adjustments.
Tillers are designed to be lightweight and maneuverable, which makes them extremely suitable for working in limited areas, such as vegetable gardens, gardens, and, more generally, small plots of land. The engines that equip the tillers range in power from 1.5 kW in lighter models up to 7.5-11 kW for more professional models. Combustion-engine models are more powerful and suitable for more demanding terrain, while electrically powered models (via mains power or thanks to batteries) are ideal for less intensive work, thus on not difficult and small terrain. Power tillers are equipped with a pair of handlebars that can be adjusted in height and direction so that the vehicle can be conveniently steered along the desired path. The few controls, generally located on the handles of the handlebars, basically concern starting the rotor and adjusting--by hand throttle--the speed of rotation of the hoes. Some models have reverse motion of the working parts to facilitate maneuvering in confined spaces. On the other hand, there must always be a special control, usually located at one of the two handles, which acts as a safety switch for the motion: it works with " dead man" logic because if released by the operator, it causes the machine to stop immediately, to avoid accidents that are sometimes unfortunately even fatal. Given its architecture, it is evident that the motor hoe is a highly specialized machine; in fact, little equipment is available on the market. Among these, we can recall colters and small plowshares to be applied immediately downstream of the rotor, which allow it precisely to open at the same time as the soil is being administered, small furrows to carry out subsequent sowing in rows, and small rubber or metal wheels to be applied to the end of the rotor so as to allow the motor hoe to carry out simple operations that require traction force, such as light plowing and digging potatoes.
The rototiller. This is an agricultural machinery that tends to be more powerful and versatile than the motor cultivator and is designed to work on larger plots and on soils that are also highly tenacious. It is also distinguished by considerable multifunctionality, being able to have a wide range of working machinery that can be coupled and of equipment. Mechanically, the rototiller has a robust structure, with an endothermic gasoline or diesel engine of variable power, usually between 3.5 and 13 kW and more, making it suitable even for relatively intensive work.
Unlike the tiller, the rototiller is equipped with a motion transmission that drives a pair of drive wheels (which can be equipped with tires with ribs, or alternatively with metal cages or even with tracks, usually made of rubber), which allow it to work on various types of soil. It is equipped with a quick hitch with mechanical power take-off for coupling with various interchangeable implements, thus giving great versatility of use. The mechanical transmission is structured on a number of forward and reverse gears for a forward speed that usually varies between 1 and 8 km/h, depending on the work to be done and the operating conditions. The main models are equipped with a differential that is always engaged or with the lock engaged by the operator so as to improve the machine's maneuverability and grip. Concerning the latter aspect, to increase the adherent weight of the machine, small cast-iron ballasts (starting at 15 kg) placed inside the wheel rims or larger ballasts (over 40 kg) fixed cantilevered at the front can be applied. Similar to the tiller, the rototiller is also driven by means of handlebars, and safety devices are, of course, always present to stop the machine immediately. Another major difference that characterizes the rototiller is the 180° reversibility of the handlebars, which allows it to be used in both directions of travel, thus allowing it to be coupled with different types of implements.
The most common ones range from rotor hoes (which are, in fact, the tools thought of as the original equipment of the machine) and spading machines to mouldboard plows (also reversible) or rotary plows, furrows, power harrows, stone buriers and seed drills. For haymaking, various types of mowers (with oscillating or rotating blades), small rakes/hay rakes, and mini-round balers are available on the market.
Sweepers, shovels, snow blowers, flail mowers, and mulchers can be mounted to clean surfaces and uncultivated areas. Stump cutters, mulchers, potato diggers, trailers, and spray booms are also available. Finally, equipment for fixed-point work, such as shredders, irrigation pumps and circular saws, is also available.
Which to choose? The former is ideal for secondary tillage, while the latter is more versatile and multipurpose. For both machines, however, operating limits must be carefully considered: given the modest engine power and the limited working width of the attachments, working capacity cannot be high. With larger models, performance improves, but sometimes at the expense of driving comfort, which is more strenuous for operators, as the mass can exceed 250 kg. A further issue, again related to comfort, concerns the vibrations that the stems transmit to the operators, although more modern models have damping systems installed with silent blocks that partially mitigate vibration levels. In any case, in spite of their limitations, these small machinery continue to represent absolutely functional and undoubtedly economically viable means for niche and very small-scale agricultural realities, contributing to their profitable permanence on the market.