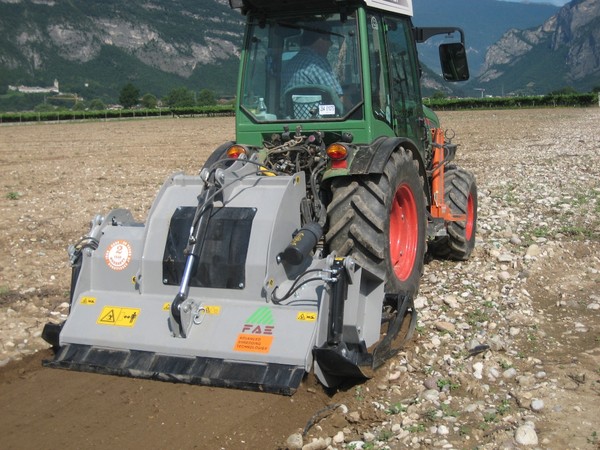
Stones - Smashed, Crushed, Pulverised
Stone breakers and pulverisers are an important addition to the farming armoury when the land is strewn with boulders and rock outcrops, but they also eat up the energy
Stone breakers are often used in forestry and road building, but they also have their role in farming when the land is rocky. This is true primarily in Sicily and Puglia as far as Italy is concerned.
When you have this type of terrain, there are three basic approaches: remove the boulders above a certain size, bury them deeper than the usual working level or break them up. In some situations, removal is inadvisable because it would change the soil profile, and finding somewhere to dump the material is also difficult. In any case, the three approaches differ significantly agronomically and in terms of energy consumption.
Stone breaking machinery can smash stones and boulders down as small as pieces only 50 cm in diameter. The power required depends on the composition of the material to be broken, the working depth and forward speed. If the depth is 20-40 cm, the power required is 90-130 HP per meter of working width at a speed of 0.15-2 or 3 km/h.
A number of Italian manufacturers make effective machinery for this type of task, for example, FAE Group, Officine Rinaldi, Pezzolato, Valentini and Kirpy. The machinery is built to be very robust, which means a lot of strain on the tractor it is linked to. Because of the weight involved, the tractor should have a high-performance rear hitch and, because of the very slow speeds of 150-700 meters an hour when rock is preponderant over soil, super-reducer gears are needed. If soil is preponderant over rock, speeds may rise to 2-3 km/h. Tractors with continuously varying transmission is also an attractive option since the on-board electronics optimises speed in the various on field working conditions, improving productivity as a result. Mounted on a three-point hitch, the stone breaker’s power comes from the PTO through a universal joint, which should have generous dimensions and must necessarily have a device to protect against overloading.
The Working Parts
A robust rotor, normally turned by one or more pulleys linked to a jackshaft through strong toothed belts located on one or both sides, functions transversally in the forward direction. There are different smashing tools, with different shapes made from material of differing hardness. You may find hammers like those found in a chopping machine, but much stronger and fixed rigidly to the rotor or hinged on it. The areas that come into direct contact with the rock have a rectangular profile with smooth angles, and are made of Hardox or other types of very fine steel, such as tungsten carbide. Toothed tools with a flat or sharp profile are used for stickier soil, but fixed teeth with diamond-studded tips are also fitted for extreme uses. This enables the machines to work even on full rock, although this implies taking account of accelerated wear, slower working speeds, and a large increase in the energy consumed.
Transmission and Housing
The stone smashing components have a smashing chamber consisting of a robust housing made of anti-wear material. Its position can be regulated hydraulically and, by varying its distance from the working parts, you can increase or decrease smashing time, consequently changing the dimensions of the final crushed stone.
The jackshaft receives power from the PTO and transmits it perpendicularly to two counterpoised shafts linked to pulleys on the ends of the rotor. Various transmission ratios can be configures according to what needs to be done. Even the PTO speed is standardised at a fast 1,000 rpm, robustness and a transmission ratio of about 2:1 are needed to handle the very high levels of torque.
To guarantee an adequately long working life and contain the noise as much as possible, the external housing is usually made of ductile cast iron and contains a cemented carbon Gleason-cut spiral bevel gear. The bearings are bevel rollers capable of tolerating significant axle loads, while lubrication is permanent with synthetic oil. The shafts are in carbide steel and large enough to resist heavy loads, and above all high torque peaks.
Soil Characteristics
In agronomic terms, increasing the fine part of the rocky content implies a percentage decrease in organic substance and, if the smashed rock is of lime or chalky origin, an increase in pH. Apart from an immediate addition of significant amounts of organic substance, one or two years should be allowed to pass before planting the cleared ground with, for example, new vineyards or orchards, giving enough time for the area to re-establish a correct water and organic balance with the formation of humic acids. It is a good idea to go rock smashing in the summer months above all, both because it is easier to work the ground when it is dry, but above all because later ploughing and the autumn rain will promote mixing of the soil’s substances.