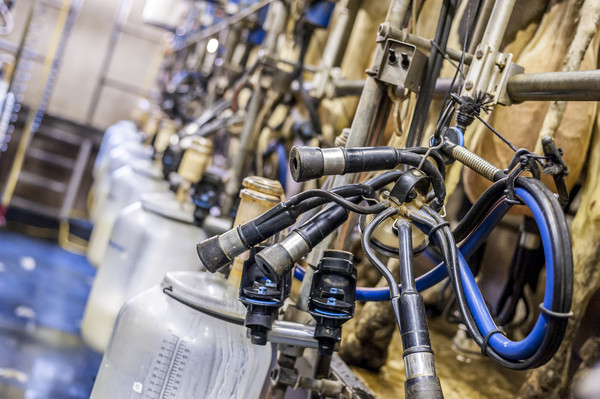
Sensors for precision milking
Sensors implemented on milking plants and robots are a valuable aid to modern livestock farm management. Such sensors ensure not only economic and environmental sustainability but also the safety and quality of barn processing and the final product
|
Precision Livestock Farming is the implementation of engineering technologies and methodologies to monitor, model, and manage animal production, reproduction, welfare, and health. Its premise is well known: the numerous and complex technical, economic, and regulatory requirements surrounding livestock production, as well as the establishment of ever-larger herds, have, in fact, forced farmers to introduce automated systems on the farm to monitor and manage key production processes. The main purpose is to satisfy both the interests of livestock farmers and the expectations of consumers in order to bring to market livestock products obtained by methods with reduced environmental impact and high standards of animal health and welfare. All of this at affordable prices. Thus, the essence of PLF is to enable the management of livestock farming through an integrated system of sensors and software that allows automatic monitoring of machines and animals. The data collected is processed and stored in appropriate farm information systems with the aim of refining the farmer's decision-making ability.
PLF devices that can be implemented in a dairy herd are many, but in general, they fall into 4 macro-categories: a) sensors for the qualitative-quantitative evaluation of the milk produced; b) sensors and methods for verifying udder health; c) devices for monitoring fertility, mobility and, more generally, the health of the cow; and d) systems for monitoring the quality of the feed ration and its efficiency. As far as the first two categories are concerned, until a few years ago, the chemical laboratory was the only way to obtain information regarding milk quality and udder health of cows: this procedure was (and still is) complex and impractical. Indeed, it is necessary to collect samples at the farms and transport them as quickly as possible (and under optimal storage conditions) to the testing site, then wait for the response. This procedure, which is certainly capable of providing more than reliable results (in fact, the laboratory can be considered the "gold standard" for the reliability of results), nevertheless lacks timeliness: it is one thing to wait for a qualitative analysis of the milk in terms of nutritional components, and quite another to make a diagnosis of mastitis, which requires the earliest possible sanitary treatment.
Sensors for measuring milk production. In the early days of mechanized milking, the only component capable of measuring each cow's individual production was the measuring jar installed at each milking post.
In the earliest versions, the container was made of glass and equipped with a graduated scale that indicated the volume of milk taken during milking: the farmer then took manual note of each animal's production. This was a measurement system made uncertain by the presence of foam, which made it difficult to survey the milk level correctly. Therefore, later versions implemented automatic systems such as placing strain gauge load cells under the jar, or float level gauges inside it, or even vane flow meters on the tubes that connected the various jars with the milk product. To this day, flow meters capable of real-time detection of both instantaneous milk flow and production, even on a per-quarter basis, are used in parlors and on milking robots. Before the advent at reasonable cost of electronics, the most common systems in milking parlors were constant-portion and variable-portion milk meters. In both cases, these are electro-mechanical instruments that measure either the number of emptyings of special trays containing a known mass or volume of milk or the amount of milk that accumulates in the sensor chamber through the use of floats or load cells. Today's state-of-the-art flow meters are continuous flow models in which the flow of milk is measured using an infrared array.
Basically, the milk flows through a short duct of known cross-section, preceded by a small siphon whose task is to interrupt the flow of fluid by inserting air bubbles inside (generating a slight turbulence called "plug flow"). Due to the presence of these bubbles, the infrared sensor array measures the speed at which the milk moves through the duct. The product of the measured velocity by the (known) cross-section of the duct gives the instantaneous flow of milk. Regardless of the principle of operation, all sensors used to measure flow and milk production must be certified by the International Committee for Animal Recording (ICAR), an international nongovernmental organization aimed at promoting the development and improvement of animal identification, performance recording and production evaluation of farm animals.
Sensors for measuring milk quality. NIR technology makes it possible to assess milk quality directly on the farm. Next to the milk meter, a NIR sensor analyzes each animal's milk in real time during each milking session. The analysis is based on near-infrared spectroscopy: during milking, a beam of light passes through the milk, and based on the refraction of the light, the NIR sensor determines over the entire mass of milked milk, its quality in terms of fat, protein, lactose and possible presence of blood, without the need to take samples and use reagents, and thus without having to discard any product due to pretreatment with chemicals. This is a rapid, non-destructive and non-invasive technology that returns reliable results not only regarding milk quality but also regarding certain aspects related to the health of the cow (e.g., abnormal values of the fat/protein ratio may indicate possible ketosis, the presence of blood in the milk may indicate possible mastitis or trauma to the udder, etc.). In any case, this is a technology that can be applied both in the milking parlor and in the robot; in the case of the parlor, its implementation is more onerous since an NIR sensor must be installed for each post, while in the case of the robot, one analyzer per milking unit is sufficient.
The sensors and methods for verifying udder health. To date, there are numerous systems for early detection of udder diseases, the most important of which is undoubtedly mastitis. One of the available methods is based on measuring the electrical conductivity (EC) of milk. In addition to the increase in somatic cells, mastitis also increases the EC of milk milked by the affected animal because its ionic concentration changes; in particular, compared with healthy milk, there is an increase in sodium and chlorine and a decrease in potassium. The method is relatively simple, but it is not completely reliable since the electrical conductivity of milk can be affected by exogenous factors such as temperature, lactation stage, fat concentration, milking interval and breed. In any case, such measurement carries interesting potential in predictive and diagnostic terms since this parameter can be measured automatically and continuously during milking, thus allowing constant monitoring of the health status of the cow throughout lactation. Another type of sensor, often found in robots, is based on somatic cell counts in a milk sample. This is a rather complex system in which a milk sample is taken during milking and mixed with certain reagents, which stain the somatic cell nucleus. This mix is then fed into the measuring instrument, where the somatic cells are counted using a fluorescence electron microscope, returning their value to the farmer. A further method, always particularly implementable in robots, involves analyzing milk viscosity, which tends to coagulate in the presence of mastitis. Moreover, this principle is already widely exploited by milkers for disease diagnosis. Technologically less complex than the previous one, this system is based on measuring the viscosity of a given volume of milk mixed with a reagent. The detected value is correlated with the number of somatic cells present expressed in cells/ml of milk. The frequency of sampling in both solutions shown varies according to the cow's health status. This allows analyses to be performed only when necessary, thus saving on reagent costs.