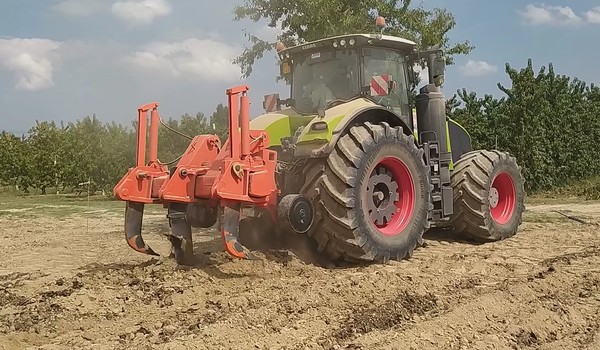
Pollutant emissions: new tractor monitoring tools
The roadmap for reducing emissions from engines installed in agricultural tractors has reached Stage/TIER 5. Compliance with this regulation is determined based on predefined work cycles, which however cannot accurately reflect the variety of operational conditions. Only dedicated predictive models can provide correct indications of the environmental impact
Air pollution has multiple causes, but a prominent place in the dock is undoubtedly occupied (rightly or wrongly...) by the gaseous pollutant emissions of vehicles equipped with internal combustion engines, especially those powered by fossil fuels.
Almost 30 years ago, it was decided to limit these emissions by establishing a common agreement in Europe and the USA for a “road map” that would require manufacturers to produce engines with a much lower impact on the environment. Hence the European emission standards commonly referred to as Euro 1, Euro 2, Euro 3, Euro 4, Euro 5 and Euro 6 for Light Duty Vehicle standards, and “Stage” and “TIER” for for non-road diesel engines, the latter also including agricultural vehicles such as tractors and self-propelled machines.
It has been a demanding, expensive and in some ways complicated process, yet with a striking result: consider that a Stage V tractor, which is the level to which engines installed on new models on the market must comply, emits only 2% of the pollutant gases compared to a vehicle with an engine of the same power compliant with Stage I. This means that a single Stage I tractor pollutes as much as 50 Stage V tractors.
If we consider that the tractor fleet in Italy is, on average, over 25 years old, it is easy to imagine how replacing an old vehicle with a new one can provide an incalculable environmental benefit. However, compliance with increasingly stringent environmental regulations has forced manufacturers to undertake a demanding technological development to contain emissions, which, on the one hand , has led them to modify the combustion parameters of diesel engines and, on the other, to provide additional devices downstream of the cylinders, to purge the harmful components from exhaust gases (see box).
Standards and operating cycles. Conformity to the various Stage and TIER levels is established on the basis of a series of regulations developed jointly by the European Commission and the Environmental Protection Agency in the United States, which are based on specific (and presumed) operating cycles of the engines that equip vehicles intended for non-road use.
This choice is understandable, since it is the only way possible to objectively establish whether or not a given engine meets the desired requirements. Furthermore, it makes it possible to immediately determine whether a certain engine is better than another, since it produces less pollutant gases.
However, operating cycles are almost never an accurate indicator of the actual use of an off-road mobile vehicle, since the modes of use can be so many and varied. This consideration is even more valid for tractors, whose versatility of use is their strong point. In fact, there are truly numerous variables that can influence this: first of all the duration of the actual work and the average power used, but also the state of wear of the engine, the level of maintenance, the quality of the fuel, the driving style, etc. And that's not all: in agriculture, the variety of mechanized processes that can be carried out within the production chains is extremely great; it must also be taken into account that the classic agricultural tractor is also used in numerous other parallel sectors, such as forestry, green maintenance, road maintenance, quarrys and the construction sector, for snow clearing, etc. Thus it would only be possible to determine the actual environmental impact in terms of gaseous pollutant emissions to a sufficient degree by contextualizing the use of a certain vehicle as accurately as possible. The aforementioned problem was posed to the Department of Agricultural and Environmental Sciences of the University of Milan in order to define in the greatest detail how much tractors actually pollute for some typical scenarios, with the final objective of creating a series of models to ascertain, in a given operating situation, which tractor was the most “economical” and at the same time the most environmentally friendly.
Initially, we focused on the viticulture sector, both because the cultivation operations are generally well defined in their execution and in the workloads required, and because the tractors used are medium-low power, for which it is notoriously more challenging to develop low-polluting engines.
The procedure. Starting from the so-called "operating points", that is the operating conditions (assumed to be constant) of the tractor engine in a certain process, models of the above-mentioned supply chain were created, attributing to each identified operation a certain duration in hours, within the entire growing season.
Based on this scenario, it was then easy to simulate, at a fixed point and with the aid of an electromagnetic brake, the workload for each process, and to obtain the desired data (i.e. specific torque, power and consumption).
At the same time, the quantity of pollutants produced was measured under these conditions with particular attention paid to the components with the greatest impact on diesel engines, namely nitrogen oxides (NO and NO2) and particulate matter (PM).
The efficiency of the engines … Obviously, even with equal compliance with the limits of a given emission stage, the engines mounted on tractors are not all the same, because each of them is characterized by different efficiency values, or specific consumption (which is the direct inverse of efficiency). In practice, it shows its ability to transform the chemical potential energy contained in a fuel into useful work when it is burned (together with an oxidizer, which is the oxygen contained in the air) in an internal combustion engine.
…and the quantity of pollutant gases produced: to highlight the differences in performance at a glance, a colorimetric reference was adopted, utilizing the so-called “traffic light” scheme (often used, for example, for houses and household appliances), thanks to which the regulatory limits (measured in terms of g/kWh, or, the mass in grams of each pollutant compared to the energy developed by the engine in kilowatt hours) were compared with the experimental values obtained.
Some results: by way of example, the results recorded are shown - both in terms of specific consumption and pollutants produced - for some vineyard tractors, theoretically used in the same way, in accordance with a real scenario, in a wine-growing company based on a 10-hectare cultivated area.
With all operating conditions being equal, the differences encountered are significant, especially for those jobs that require limited power. The average values, weighted according to the actual duration of use, vary between 226 g/kWh for the most energy-efficient model and 303 g/kWh for the least efficient one: an increase of as much as 34%. For individual operations the gap is sometimes even greater: for example, for trimming it goes from 233 to 342 g/kWh: an increase of over 46%.
Moreover, the color-coded classification makes the different conditions very clear: tractor 2 is relegated to class G (red), while vehicle 4 is brilliantly placed in class A (green). It is therefore clear that choosing one tractor instead of another means saving considerably on operating costs, at least as far as the “diesel” item is concerned. If we consider that this modus operandi has in fact been replicated for a considerable number of years, we can understand the importance of the best choice in terms of operating economy of the best tractor model within the wide market offering.
Even with regard to the environmental aspect, it is worth choosing the most appropriate tractor carefully: compliance with the emission level already greatly influences the quantity of gaseous pollutants emitted, but the simulation of real use adds further useful information, and also shows some surprises. It goes without saying that the technical evolution of the diesel engine over the last few decades has played a big role in the process of reducing pollutants: the widespread introduction of electronic control, injection, turbocharging and even more so the common rail have improved the situation enormously, especially reducing the production of unburned hydrocarbons and particulate matter, but with the entry into force of increasingly restrictive emission limits it has been necessary to resort to further technical interventions.
Real assessment of pollutants: the models from the realistic scenarios described above were applied at the Department of Agricultural and Environmental Sciences of the University of Milan, and their emissions were then compared to the regulatory limits established by the Stage (or TIER) of approval of the engines examined. Again with particular reference to the tractor models used in the vineyard, a contrasting situation emerges, showing excellent containment results for those pollutants upon which the specific devices act, whereas the limits are exceeded for other, sometimes quite significantly. In fact, if an engine with a particulate filter is installed, CO and PM emissions are practically zero, but HC and especially NOx are extremely high. The opposite situation occurs when only the SCR is installed, which limits NOx very well, but cannot effectively act on PM.
The current regulatory level for engines installed on tractors, which recently came into force (Stage/TIER 5), has resolved this discrepancy. In order to comply with this level, the majority of engines currently mounted on agricultural tractors newly placed on the market must be equipped with two (and sometimes even more...) anti-pollution devices.
Predictive models: in addition to the regulatory limits based on standardized usage cycles, the progressive development of predictive usage models specific to one's own production situation will be able to provide valuable information to users and effectively guide them towards the selection of the tractor most suited to their needs, with attention to the economy of operation in terms of fuel consumption, but also to the reduction of the environmental impact in terms of gaseous pollutant emissions.
Strategies and devices to reduce gaseous pollutant emissions
In the mid-1990s, specific parallel regulations were issued (referred to as "TIER" in the USA and "Stage" in Europe), aimed at the progressive reduction (through successive steps spaced out over time) of gaseous pollutant emissions produced by internal combustion engines, in relation to the maximum power of the engine and the sector of application. Attention was focused on four substances, namely carbon monoxide (CO), unburned hydrocarbons (HC), nitrogen oxides (NOx) and particulate matter (PM). For diesel engines, it was especially important to contain NOx and PM emissions. To reduce gaseous pollutants, action was taken both by limiting their formation in the combustion chamber and, above all, by inserting various types of filters downstream of the engine to physically block them and/or catalysts to render them chemically harmless. In fact, recently both strategies have been increasingly used. It is significant to underline that the Stage V (Tier 5) level, now required for engines installed on agricultural machinery, has reduced the environmental impact of the pollutants mentioned by up to an incredible 98% compared to Stage I engines, the limit in force initially.
Technical methods for reducing pollutants
EGR (Exhaust Gas Recirculation)
Exhaust gas recirculation (EGR) is a solution based on the re-introduction of a portion of the exhaust gas (approximately 5-15% in volume) into the combustion chamber, thereby lowering the combustion temperature and consequently reducing the production of NOx.
This process is usually carried out externally, with the interception of a variable part of the exhaust gases by means of a special electronically-controlled valve. The gases are then cooled through a heat exchanger to reduce their temperature and increase their density. They are then re-introduced into the combustion chamber together with the diesel fuel and combustion air.
SCR (Selective Catalytic Reduction)
This method makes it possible to effectively reduce the NOx level through the subsequent treatment of the exhaust gases after they are generated, and thus without interfering with combustion. Inside a catalytic converter, and in a manner controlled by a special electronic control unit, a 32.5% pure aqueous solution of urea (often commercially referred to as "AdBlue") is vaporized and placed into the exhaust gas flow. At high temperatures, it dissociates, releasing ammonia. The latter, together with oxygen, combines in the catalyst with nitrogen oxides, giving off atmospheric nitrogen (non-toxic) and water, in the form of steam.
DPF (Diesel Particulate Filter)
This is a physical filter made of extremely selective refractory material, which manages to trap larger particles on the typical section of its lattice. Periodic cleaning of the DPF (called “regeneration”) can be passive, occurring when the temperature of the exhaust gases is particularly high, or active, with the modification of the combustion of the diesel fuel, in order to raise this temperature to trigger the combustion of the carbon particles trapped in the filter with a corresponding reduction in terms of average size and their consequent expulsion.
DOC (Diesel Oxidation Catalyst)
The diesel oxidation catalyst (DOC) acts on unburned hydrocarbons (HC) and carbon monoxide (CO), which are converted into CO2 and water vapor. DOC is made up of a honeycomb ceramic matrix, upon which a thin layer of noble metals (platinum, palladium, rhodium) is deposited, which act as catalysts to facilitate the appropriate chemical reactions in an accelerated manner.