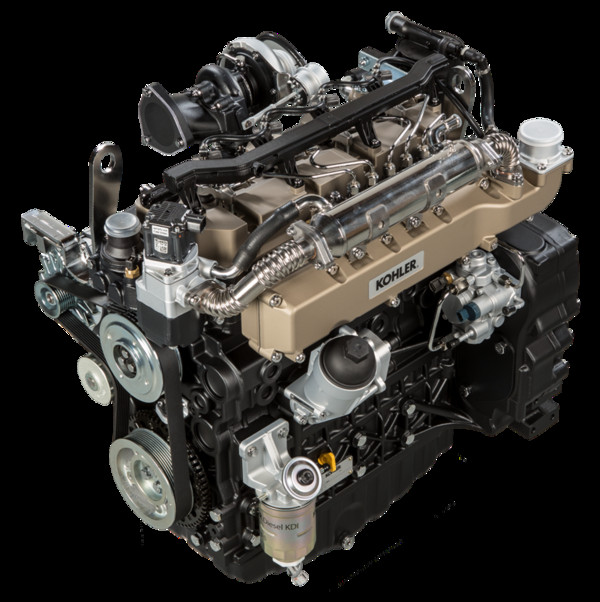
Performance and versatility with Kohler KDI 3404 engines
The Kohler KDI engines are moving on from their success at EIMA International to the SIMA Agricultural Business Show in Paris for the presentation of the all new KDI 3404 (Kohler Direct Injection) diesel engines. These power plants are equipped with such advanced technologies as a high-pressure (2000 bar) Common Rail system of the latest generation, an electronically controlled EGR valve for the circulation of the right amount of exhaust gases – are liquid-cooled with second stage water/air heat exchanger – and a 4 valves per cylinder system designed to house the injector in a perfectly vertical position at the very center of the combustion chamber, a solution which optimizes fuel filling, atomization and mixing with oxygen in the chamber for reduced fuel consumption and power equivalent to that of larger displacement engines. The new Kohler KDI 3404 engines, available with power ratings of 56 kW and 100 kW, are built with no particulate abatement systems (such as DPFs) which means lower fuel consumption and longer maintenance intervals, since no filter regeneration is required. They are, however, equipped with a sophisticated electronic management system which guarantees a smooth and immediate response to load and noise and vibration limited to a minimum. Kohler KDI engines over 56 kW are equipped with Selective Catalyst Reduction (SCR) for the abatement of NOx exhaust gases for the compliance of these engines with EU emissions regulations Stage IV – Tier 4 Final. Getting into the details of the technologies, to be noted is the combination of the most advanced common rail system with a high pressure pump which operates at 2000 bars with G3S solenoid-type injectors, for the precision dosage of fuel injected, and with the electronically controlled EGR valve exhaust gas recirculation system which consists of two cooling stages – liquid cooling and water/air heat exchanger – that optimize heat exchange without increasing overall size of the size of the compact engines. Also, the EGR valve location on the hot side effectively prevents it from jamming, which ensures maximum reliability. Another significant detail is the architecture of the 4 valves per cylinder system designed to house the injector in a perfectly vertical position at the very center of the combustion chamber for precise fuel filling, atomization and mixing with oxygen in the chamber. Yet another strong point of the KDI 3404 is versatility made possible by a total of four different power outputs for four PTOs, with two additional PTOs at the sides (SAE A and SAE B). The PTOs supplement the main and secondary take-offs designed and positioned to draw the greatest amount of power from the engine for maximum flexibility.