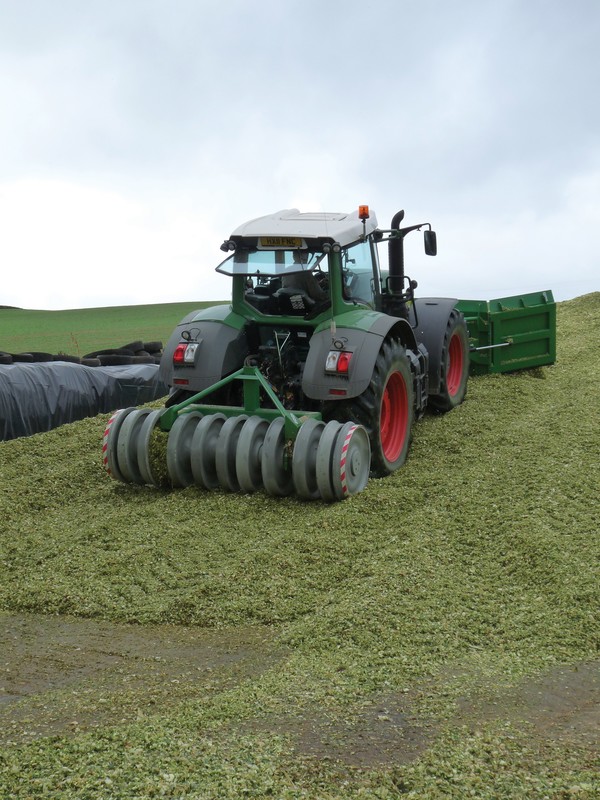
Mechanical technologies for preservation of forage
Placing the forage in the silo is an apparently simple task, but it must be done taking into account a few precautions, better still using dedicated equipment, in order to ensure the best conservation of the product
The preservation of fodder is basically based on two techniques with completely opposite objectives: the traditional one, i.e. haying, requires the material to be dried at a specific humidity level so as to avoid it being degraded by bacteria and moulds. This is the solution that is adopted for many other edible products intended for human consumption, such as grain cereals.
Conversely, for several decades now the ensilage alternative has imposed itself, whereby the product (32-35% of dry matter, in the case of corn) is compacted into heaps (or even bales) and then segregated from the external environment, so that the oxygen trapped in the mass is quickly depleted by the presence of aerobic bacteria, thus creating an anaerobic environment and stabilizing everything for proper preservation, which can last several months. In particular, this second option has been refined for shredded corn, and has had a further impetus in recent years due to the use of silomais as the basic ingredient of the mass intended for anaerobic digestion in biogas plants.
Trench silos
From the vertical cylindrical silos (the so-called “cremasco silo”, with all its subsequent evolutions), silage containers have quickly evolved into simpler horizontal, flat, pit or trench structures. The latter are by far the most common in Italy, and feature a concrete platform, completed by two side walls and generally an end wall, in prefabricated concrete elements. This creates a rectangual pile, duly fitted with a plastic cover (weighed down with tyres, stones, gravel, etc.), whose top is curved so as to help drain away rainwater.
Filling the silo
Regardless of the starting quality of the shredded corn (it may be useful to break the grain in advance, to facilitate the leakage of the cellular juices and thus start fermentation), the placement of the shredded grain in the silo is no doubt a key operation for the optimal preservation of the plant material, being essentially aimed at filling the available volume adequately (without unwanted air pockets), while expelling from the mass as much air (or oxygen) as possible. This result, which at first glance is easy to obtain, must, however, carefully take into account some important precautions (see box).
Machines for constructing the pile
It is quite obvious that in this case the key factor is weight, so self-propelled vehicles that are high-powered and therefore considerably heavy have to be used, and they must be equipped with devices for moving and positioning large quantities of product.
Contrary to what you might think, agricultural tractors are not the only devices used for this purpose. Telescopic lifts, excavators and even crawler vehicles designed for other uses (e.g. the so-called “snowmobile”) are used, repeatedly moving on top of the silo, shifting the shredded grain to give the desired shape to the pile while compacting it.
In any case, the tractors must be equipped with devices to carry/move the shredded grain.
These are sturdy concave vertical shovels or blades, similar to snow plough blades, as the handling operation is the same.
Proof of this is the fact that several manufacturers of snow blades also offer this equipment, often featuring the same functionality.
The shredded grain blades are usually attached to the lift’s three-point hitch. Even though rear models are available, there is no doubt that the most efficient combination is the coupling to the front lift, which provides better visibility while perfoming the work.
The working width and the weight are significant, up to 4 m or more, with a mass of over 1000 kg. Larger models have lateral wings that can be folded hydraulically, designed to contain more effictively the mass of product to be moved.
The wings are also completely foldable, to fit into the shape for public road transport.
Some models also offer the ability to tilt the entire blade sideways to facilitate positioning the material on the edges of the silo.
The blades are generally equipped with rollers (pneumatic, full rubber or cylindrical in full or hollow steel) for resting them on the material to be moved/compacted.
For greater wear resistance, the lower part of the blade is sometimes made in Hardox, while to provide the operator with adequate visibility of the product, there is always a grid (or a non-continuous surface) on the upper part.
The preservation of the com silage
There are generally four distinct phases:
1. initial aerobic phase: it begins with the shredding and continues during the preparation of the pile. The residual air trapped in the mass causes the growth of aerobic microorganisms, which consume oxygen and sugars and produce carbon dioxide and heat (increasing the mass temperature);
2. main fermentation phase: borne by the carbohydrates, which causes a reduction in pH (from an initial value of 6 to less than 4);
3. phase of anaerobic stabilization: the fermentations cease due to the absence of oxygen in the mass, with a simultaneous development of anaerobic microflora;
4. consumption phase: the silo is opened on its front side, letting air in. The oxygen stimulates aerobic microorganisms, in particular yeasts, acetic bacteria and moulds.
Therefore, the silo must be loaded as fast as possible, although it is very important to pay attention to the compacting density of the vegetable mass, which may vary from just over 100 to almost 400 kg/m³ of dry matter (DM). Logically, the more compact the pile is, then less DM will be lost: especially during the first 6 months of retention, there is an inverse proportion ratio between the pile’s density and the DM losses In practice, if the density increases, for example, from 160 to 320 kg/m³, the DM losses are halved.
Another important aspect is the intensity of day-to-day silage consumption, that is, the advancing speed of the trench collection front, which should be around 1.5-2.0 m per week. This entails a careful design of the size of the silo in relation to the needs of the herd.
Thorough compaction
The appropriate placement of the material in the silo, the weight of the tractor itself (or another towing device used for this purpose) coupled with a sturdy blade, and the repeated passes over the material are sufficient to achieve the desired shape and degree of compaction of the shredded grain pile. However, it is possible to operate even more effectively with other devices specifically designed for this function.
The German Reck GmbH offers the Jumbo II, a spreader specially designed for grass silage. In practice, this is a large roller of sturdy sheet metal of about one metre in diameter rotating in reverse of the direction of movement. Jumbo II has a width varying between 2.25 and 3.10 depending on the models, and it has 56 or 58 blades welded to the outer surface shaped to direct the product. To better direct the shredded mass to be stored, the roller can also be rotated obliquely on both sides by 20°.
Especially in Anglo-Saxon countries, specific full-disk compactors are rather widespread, to be coupled to the front or rear of the tractor. These heavy disks, 50-60 cm in diameter, rotate freely on a sturdy pin, supported by a chassis that attaches to the three-point hitch.
The English company Kelvin Cave Ltd offers the SilaPactor, in a range of models of different widths, from 2 to 4 m, logically with a significant mass of between 2500 and 6000 kg.
Thanks to the specific tools, the additional weight of the equipment and the working width (far higher than that of the tractor’s tyres), the manufacturer states that it is possible to increase the compaction efficiency by 25-40% with a number of passes up to three times lower than the traditional system carried out with the tractor tyres alone, thus saving work time, diesel fuel and machine wear.