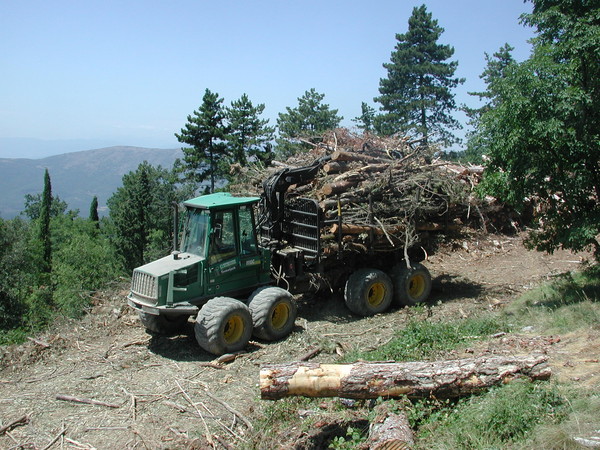
Forestry: types and models for specific mechanization
Mechanical engineering industries manufacture a wide range of machinery for work in the field of forestry. Systems for harvesting timber and biomass have become increasingly technologically advanced but the choice of machinery depends on the specific requirements of the worksite and environmental conditions in which operations are performed. Important new developments have been achieved through the collaboration of the specialized industries and university and research institutes
Systems for harvesting timber and biomass in Italy work through a dual market. On one side are small agro-forestry entrepreneurs who find it essential to deploy flexible machinery for use in agriculture as well as forestry and on the other are enterprises specialized in forestry which for some time have been oriented toward the acquisition of advanced and highly productive machinery. In Italy, the usual combination for felling trees for clearcutting is an agricultural 4WD tractor and a forestry trailer equipped with a boom and a log grapple whereas the specialized forwarder is used much less. For example, in north Italy there are 1,366 tractor-trailer units compared to only 48 forwarders. When it becomes necessary to operate on sloping land with limited access and maneuverability it can be useful to stay in the middle of the road between the two arrangements, relying on agricultural machinery as well as such as the advanced equipment of a forwarder, possibly flanked by an industrial chipper.
For the production of chips beginning with the byproducts of operations it is important above all to set up the worksite to limit the downtime of the most expensive machinery. The forwarder features winning agility and load capacity compared to the tractor and trailer combination on difficult worksites and in adverse weather conditions and can be used to move residues from the woods to a nearby location accessible to transport machinery. On the other hand, tractors coupled with bins with high sides can directly load chipped wood from the chipping machine, perhaps a model with an independent engine towed on the tractor track, and work as a shuttle to unload the product in a cleared area. The chips accumulated in this location can then be loaded on trucks for transport to a central location while avoiding downtime for the heavy equipment. Once the chipper has completed operations along the track it is moved to the cleared location to begin chipping the materials brought in by the forwarder.
Forwarders are built for greater mobility, stability and ergonomics but, this said, tractors with forestry trailers hitched on are still widely used for moving timber due in part to their speed on the road. The fastest forwarders on the market are now in use in Italy, especially in alpine areas. Among forwarders comparable for power and load capacity and agricultural tractors widely used in forestry – models at 100 kW coupled with a 2 axle forestry trailer equipped with loader – there are models such as the 3 axle Welte 130T at 113 kW and the 4 axle HSM 208F at 130 kW of power and a 10 ton load capacity. The owners of forwarders report that the machines are used some 1,301 hours annually compared to 717 hours for tractors with trailers.
It must be taken into account that forwarders are not stopped by rain or snow as are tractors and that their productivity is 27% greater and fuel consumption is 50% higher. Without considering the environment in which they work, if used for clearcutting and the transport of timber, forwarders operating in Italy cover long distances, three times greater on average than those put to use in Nordic countries where they originated. This is why the models deployed in Italy require more speed to avoid lowering productivity and efficiency on the worksite.
Still on the issue of moving timber, Italian manufacturers are attempting to find alternatives to the traditional tractor and trailer combination – for farming as well as forestry – and have come up with a version of a forwarder adapted for Mediterranean woods. An example is the Bernardi B248 which combines efficiency and performance with a 247 Hp Common Rail engine and a hydraulic-mechanical transmission allowing road travel at a maximum speed of 36 km/h. The 350 liter hydraulic oil tank and an efficient cooling system make certain that this Made in Italy forwarder will not overheat covering long distances on the open road. The loader also features a net load capacity of 12 tons, a reinforced cab and a double extension crane plus a moduable width according to the tires mounted to make of the machine an excellent model for forestry work.
On the issue of combined felling and clearcutting operations, selective tree removal and plantation planting, with valuable species or tree ranks for example, CNR-Ivalsa conducted field trials in 2013 on two harwarders, machines combining harvester and forwarder operations. The objective was to increase efficiency in an operation involving only one cost because of the low financial worth of the materials brought in, that is, firewood and chips. The trial was set up by CNR-Ivalsa, the University of Udine and the Friuli Venezia Giulia Region associated with the Arboplan and INFRES Projects. Two harwarders were tried out in the field: the first designed for thinning and the second, more powerful, built for work in other forestry settings. Used for the first case was a Vimek Biocombi 610 with 6WD a 44 kW engine, weight of 4.9 t and a 5 t load capacity. The Vimek is equipped with a crane with a 5.2 m boom with a grapple saw with a storage function. Moreover, the platform is fitted with stanchions for compressing the load. The other machine was a Pfanzelt Felix 206 with 4WD, a 130 kW engine, and a crane with a boom of 8.5 m. Various models of heads could be mounted on the crane and a Logmax 5000 was used for this specific case. The load platform can be extended for a load capacity of 10 t. Whereas the Vimek Biocombi can fell and immediately load the log on the platform, the Pfanzelt Felix 206 requires a change to a grapple head for handling trunks. The two machines were tried out for the production of two assortments: entire trees pollarded and sectioned in lengths of 3-4 m plus the lops carried out separately and stacked on the side of the road. The tree tops and sections were then chipped on the roadside by a Pezzolato PTH 1200/820 Hackertruck rated at 390 kW. The smaller harwarder was shown to be more efficient for felling and loading whereas the larger machine was better for moving the materials from the woods to the road. However the difference in the productivity between the two machines was only 5%. Productivity averaged out at 3 t/h for log sections as well as for the tree tops.
The total cost of the harvest, including chipping, came to between 24 and 39 €/t respectively for the Vimek and the Pfanzelt. The former harwarder made it possible to bring in savings from 15% to 20% compared to the traditional system whereas for the latter the costs were similar but, with the advantage of being type-approved for circulation on public roads, as is the smaller machine, this one led to savings in moving from one worksite to another. The Vimek is advised for thinning operations on small plantations whereas the Pfanzelt is the choice for stands of larger diameter trees and covering longer distances. An example of innovations in the sector of machinery for work in the woods is provided by the prototype of the processor for the European Union SLOPE Project – integrated processing and control systems for sustainable forest management – in which CNR-Ivalsa is a partner. This machine, based on an ARBRO 1000 processor extension, is equipped with highly advanced sensors for identifying the quality of the trunks while they are being prepared. Among then is a spettrophotometric camera (NIR, IR and RGB) and a laser. Thanks to (UHF RFID) electronic tags it will be possible to associate the standing trees with felling recommendations which the processor carries out for achieving the highest value of the timber assortment. The processor can, moreover, tag each trunk with a new label identifying it with a quality classification. All the information produced on quantity and quality of the products is made available in real time via a remote server for the management of operations, information which can be used for online auctions of the round-timber just produced. Obviously electronic tagging also enables total traceability of the materials: for each single trunk it will be possible to trace it back to the standing tree from which it was produced.