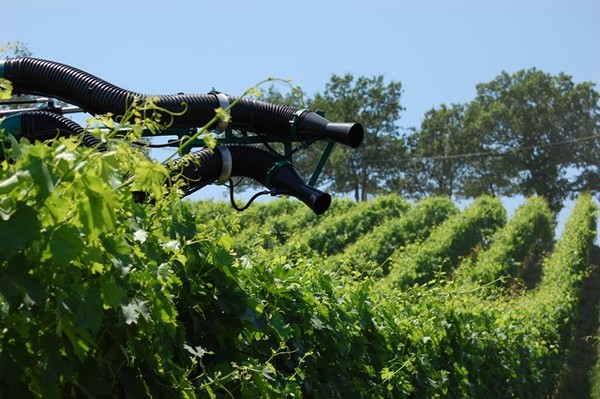
Evolution in Spraying: Cutting Drift
In Italy as elsewhere, substantial amounts of pesticides and the like are still sprayed on crops of all kinds in a serious threat to the environment, so sprayers that can couple efficiency and eco-friendliness by achieving precise regulation of the air and liquid they use remain high on the agenda of farm machine manufacturers
About 140,000 tons of about 350 plant protection products and pesticides are sprayed on Italian crops each year, according to the national health institute, ISTISAN. About two-thirds are fungicides (about 87,000 tons), and the rest includes herbicides (about 15,000 tons), pesticides (18,000) and miscellaneous substances (20,000). These are large quantities and lead to a well-founded suspicion that large amounts could be dispersed into the environment if spraying is effected incorrectly. Efficient and correctly regulated spraying equipment is an absolute necessity.
The Situation
The main aim in rationalising the distribution of plant protection products is to ensure that the products hit the target as much as possible, minimising drift, which depends on the type of spraying. Thanks to their forward speed, the boom sprayers used for herbaceous crops leave a trail created by the drops as they leave the nozzles. The drops tend to float in the air for a period of time that varies according to the weather conditions. The trail is a zone of ‘potential drift’, which becomes actual when a side wind blows the drops outside the intended target area.
Orchards and vineyards are usually sprayed from below, using the upward airflow created by the machine’s blower. The spray flow can easily pass through the crop and beyond, dispersing in the environment. If the present state of crop spraying is worrying, or even critical, it is so above all in the case of fruit trees and vines. The target plants rarely get more than 50% of the spray from traditional sprayers, and in many cases this proportion of dispersed spray may rise as high as 80%. Whether by drift or dripping, what is lost ends up by damaging sensitive plants and contaminating the surrounding environment, even at some distance from where the spray was applied.
If this is the situation, it is only too understandable that sprayers are needed that achieve precise calibration of the two main components, air and water, involved in drift: water in terms of the amount sprayed on each unit of surface area and drop size; and the air that transports the drops in terms of volume produced and flow direction.
Sprayer Types
Sprayers can be classified by function and construction, how the spray is created and how it is carried to the vegetation.
There are sprayers that create the spray by hydraulic pressure or pneumatically, and the drops are carried towards the target by kinetic energy (projected jet) or air-assisted. If you combine the two parameters, you get: pressure sprayers, typically the spraying booms used for herbaceous crops;
air convection, most sprayers applied to tree and herbaceous crops with an air sleeve guiding the air flow; pneumatic, little used, and almost solely in vineyards.
Each type offers different risks for dispersal by drift if the devices are applied inappropriately. Pneumatic spray production tends to generate drops smaller than the type from hydraulic pressure, and air assisted spraying can spray off target if the airflows are of the wrong size or directed wrong. To minimise pollution risks, sprayers must have the equipment to make calibration as precise as possible in terms of the crop to be sprayed and the spray mixture to be applied. A choice has to be made on some fundamental operating parameters such as volume per surface unit, typically litres per hectare, and the right degree of pulverisation to avoid, as far as possible, the formation of an excessive share of fine droplets (indicatively, diameter less than 100 micron) since they hang in the air and are more easily blown beyond the target area by the wind. For air aided and pneumatic models, precise calibration is also needed on the quantity of air the blower produces and the direction of the air flows.
Innovation in Spray Booms
The basic structure has changed little since spraying booms were first introduced in France and the US in the late 1800s, but various components have been improved, from the frame and tank to hydraulic circuits for the circulation of plant treatment mixtures from the tank to the nozzles.
While achieving uniform distribution is still an aim aided by on-board computers and GPS navigation systems, it is seen as less important these days than safety for the operators and the environment. Recent sprayer models include features such as automatic dosage measurement, washing of the hydraulics and the operator’s hands of the often harmful spray, and automatic filling of the spray tank without any human intervention.
Spray booms are the main feature of sprayers used for herbaceous crops. Booms can stretch along a front as wide as 48 meters (about 158 feet), although in somewhere like Italy where fields are smaller, the maximum is about 24 meters.
A spray boom has to be both light and rigid when extended in the working position. To ensure spraying uniformity and drift control, there should also be stability along and across the boom, damping out vibrations transmitted along the device when at work.
The shape of the nozzles is also crucial. They almost always use a system called air inclusion to exclude as far as possible the creation of fine droplets. They will also create a fan-shaped spray designed to minimise the effect of variations in height due to vibration, especially with very long booms for which vibration can more easily translate into falling uniformity.
Some booms have air sleeves, which ensure that the airflow achieves greater cover, improved penetration, and a chance to spray even when the wind is moderately strong. Sleeves and air-inclusion nozzles together can help a lot with drift.
It should be clear, however, that it is not always the best idea to use the sprayer’s fan to create airflow through the sleeves. Even if there is no wind, spraying fields without plant cover can be problematic. A jet of air creates turbulence, which can leave spray droplets hanging in the air for longer and lead to an increase in drift. In this case, the best bet is air-inclusion nozzles, which guarantee an excellent job in still conditions.
Another big disadvantage for air sleeve sprayers is the high cost and weight, and the fan uses a lot of power meaning that a powerful tractor is needed to power it, even for tractor-mounted models.
Spraying Tree Crops, Vines
The main factor in successful spraying in orchards and vineyards is how the air moves through the vegetation. The most recent models take this into account by focussing on fan features and how the air carrying the spray is distributed.
The airflow’s magnitude can be adjusted, and air jets can target the airflow according to the profile of the vegetation. When the vegetation has a horizontal shape as in pergola, canopy or similar training methods, spraying must necessarily be from below, but other methods are compatible with a range of sprayers.
These can range from air-assisted mist sprayers with variously shaped lateral vents, ‘anti-drift’ towers, or hydraulic or pneumatic models, the last having a centrifugal fan feeding into a manifold of rigid or flexible pipes terminating in vents or nozzles that can be placed near the vegetation to be sprayed. The idea is to get the air jet and droplet formation as close as possible to the target vegetation to minimise the amount of spray that overshoots the mark. Thanks to their lightness, these devices are also very good for spray heads on straddle frames used to spray more than one row at a time, which is also said to help limit drift and help spraying uniformity.
Straddle frames formed the basis for the development of ‘tunnel’ sprayers, whose main feature is that they can recover the spray fluid that drips off the sprayed vegetation. This type of sprayer has been developed strongly in recent years by a number of manufacturers who have put various models on the market.
Tunnel sprayers wrap the rows in orchards or vineyards between two panels, usually varying in size according to the size of the crop plant and made of polyethylene or fibre glass. The devices can be tractor-mounted or self-propelled, usually with three tunnels mounted on a powered harvester frame. Apart from the advantage of handling three rows at a time, this approach allows use of the frame extensively throughout the year.
The simplest design generally applied only for vines with limited vegetation has a vertical spray bar without a fan. But most tunnels improve penetration of the vegetation by air assistance with an axial, centrifugal or tangential fan. Some of the airflow is used to create air currents inside the tunnel designed to improve spray recovery.
Two main design features handle how the air circulates inside the tunnel. In some models, fans inserted in the panels promote air circulation through the row, move the vegetation, then help recirculate air through the plants. In others, a single fan produces horizontal and vertical blades of air designed to keep the spray drops inside the tunnel. The big advantage of spray recovery is that the volume of spray is self-regulated in terms of vegetation density, thanks to the extent of spray recovery early on when the first treatments are applied to limited vegetation growth, significantly reducing overall spray mix usage.
Recovery devices also permit an efficient use of low volume spraying with reduced drift or loss to the ground as compared with traditional sprayers. This is because the spray jets are close to the vegetation and the micro-environment is saturated in humidity. Inside the tunnel, the smallest drops reach the vegetation rather than evaporating.
How much spray can be recovered varies according to a number of factors. With tunnel sprayers, around 40% is the estimated rate of recovery, but this may rise as high as 85% in early growth spraying. The biggest winner is the environment.
The problems of tunnel spraying systems are similar to those limiting the use of straddle frames. A major issue is that neither device can handle anything but very limited gradients, which rules out many vineyards. In addition, there should be no obstacles and vine training methods such as Guyot and various styles of cordon are off limits. In any case, the operator must be very expert to avoid running into vines, trees, wires and supports. Other problems include filtering recovered spray, which is particularly problematic when the liquid includes a high proportion of pollutants. At the same time, it is also difficult to work out a priori precisely how much mix should be put into the spray tank, since the amount to be recovered cannot be estimated.