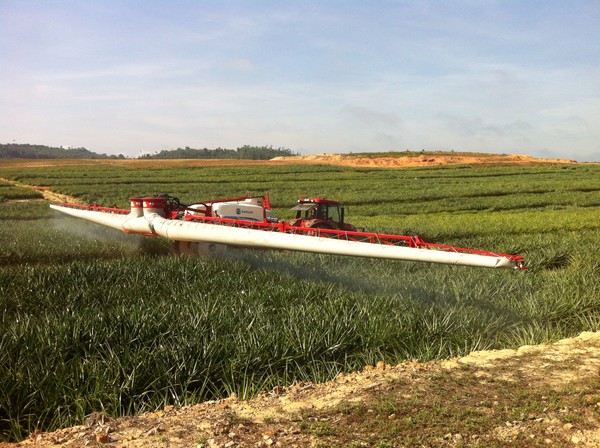
Distribution of crop protection products: the sustainable defense
For the best distribution on crops of plant protection products modern and efficient sprayer booms are absolutely necessary. New generation pressure regulators, anti-drift nozzles and sensor systems ensure an increasing scientific and measured use of chemical products and provide economic and environmental benefits
The leading objective of a farming enterprise is to achieve quality production due to the pressure of consumer demands as well as the impact on the environment of plant treatment products applied in the defense of crops. In addition there is the obvious need to guarantee maximum safety in the operations performed by farm workers. These considerations underscore the importance of a strategy for a thorough and detailed understanding of the technical and operational features of the equipment for the distribution of CPP and the best way to apply them in all conditions of operations.
For herbaceous crops the machines usually used are boom sprayers which mechanically atomize a mix of water and the active chemical ingredient and target the spray from the top down, working with gravity. Most of these machines micronize the liquid and drive it through the nozzles and in some rare cases a centrifugal reaction is used to produce droplets or an extremely fast jet of air, a pneumatic micronizer.
The most advanced sprayer booms are surrounded by a flow of air downwards to improve the penetration of the product on the foliage while lowering the drift tendency.
In any case, the main objective is always uniform distribution of the correct quantity of the active chemical as determined by agronomics and minimizing inevitable loss due to drift, evaporation of the mix sprayer and percolation toward the ground.
Maintaining the uniformity of the application is not a simple task, especially during transitory acceleration and slowdowns in the field, but fortunately there are increasing numbers of boom sprayers equipped with mechanical or electronic regulatory devices capable of automatically adjusting the quantity of the product to distribute with an increase in speed. Unfortunately, many older model of sprayers are equipped with constant pressure regulators so that uniformity of applications can only be achieved by rigorously maintaining the pre-set speed; this obviously means that in real operating conditions overdosing is inevitable when the speed of the machine slows and underdosing occurs when speed exceeds the target speed.
Moreover, it is important to keep the distance of the nozzles from the target constant, a condition made possible with stable arrays, now widespread, or rare and costly active arrays.
To maintain the quality of the spray the nozzles must be replaced periodically, especially when quantity sprayed exceeds the nominal value by 10% due to natural wear. The problem is not so much the quantity, rather the serious deterioration of the quality of the jet which in this case is producing extremely non-homogeneous sized droplets and an irregular geometry of spray.
From the point of view of duration alone, the best materials for nozzle tips are ceramics, followed by hardened steel, polymer plastics and then brass and aluminum, with the latter two components providing less performance.
The volume of the mix defines the quantity of liquid (water + formula) for application on a determined unit of area, generally a hectare; recent research has found that for boom sprayers the most suitable values for maximizing the efficiency of treatments refer to the intervals listed in table page 50.
Another important factor must be considered for optimizing plant treatment and that is the size of the droplets. The size now widely determined is that > 500 μm is the most efficient size for plant treatment compared to > 200 μm for a drastic reduction of coverage and a greater tendency to percolate.
On the other hand, though droplets of > 100 μm have potential to provide better coverage of foliage they are more difficult to control for drift and evaporation.
Thus working with well maintained modern boom sprayers makes it simple to achieve the most satisfactory results but, unfortunately, the inventory of machines in operation includes many with parts and components given scarce or no maintenance.
In these cases, even the application of the right strategies merely for spraying CCP in the field it is virtually impossible to optimize these operations.
In any case, old does not necessarily mean inefficient; dated models can often be brought into line with technological progress by mounting new generation parts and components which can be installed without the need to make substantial mechanical modifications.
Anti-drift nozzles
These are fairly recent. Pressure for spraying and amount being equal, these anti-drift nozzles create droplets of larger dimensions. There are those which inject air into the droplets produced which, on impact with foliage, break into a large number of small single liquid droplets to provide better coverage of the foliage.
All the top manufacturers on the market featuring catalogues on these components, including Teejet, Albuz, Lurmark and Lechler.
Advance sensors
Specific optic sensors have been recently developed to mount on sprayer booms capable of detecting weeds growing between crop rows to enable the machine to spray only where it is actually necessary.
The leading companies with this type of equipment in their catalogues are the Italian Arvatec with the Weed-Seeker and Green-Seeker and the Danish Eco-Dan.
On the other hand, there are specific ultrasound sensors to mount on the ends of the sprayer booms for controlling hydraulics to maintain the booms as close to parallel to the ground surface as possible.
It must be pointed out however that these self-levelling devices are rather invasive and costly.
Pressure regulators
DPM: DPM is the acronym for Direct Proportional Motor. The installation of this type of device is now standard even on so-called modern entry-level machines with electric power. Compared to obsolete constant pressure regulation, the flow from these modern pumps is directly proportional to the pump speed and the pump is equipped with a relief valve and a bypass line between the pump outlet and the nozzle shut-off valve. The pump must be capable of delivering the volume of material required by the nozzles when spraying by single sections of the boom is closed, plus the volume required by the tank agitators, plus an additional capacity of ± 20%.
DPA: means Direct Proportional Advance, that is, maintaining the CCP dosage uniform over a unit of surface throughout all variations of speed of advance. Aside from rare cases involving solely mechanical DPS regulators, most of them are controlled by CPU, central processing units, which send signals produced by flow meters, pressure transducers and a speed sensor. By now, any sprayer machine at the certain level will be equipped with DPA which is not a recent innovation but is still fairly costly. The main manufacturers which market these devices are Arag, Teejet, Agrotop GmbH, Braglia, Salvarani, Comet, Spraying systems Co., Tecomec, Udor, MC Elettronica, Imovilli Pompe srl and Protek Spraying srl.