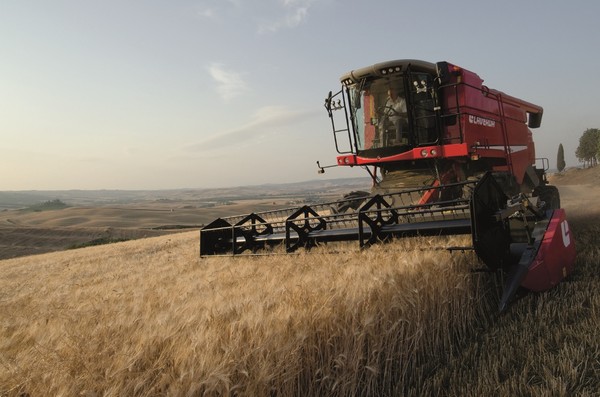
Combine harvesters: innovation for a sustainable harvest
Bringing together hourly productivity and quality threshing is still one of the main objectives of manufacturers and the need to make harvesting more and more sustainable at the agronomic level has opened onto a significant technical evolution also for the management of crop residues and soil compaction
One of the leading objectives pursued in recent years by manufacturers in the sector of harvesting machines has been to combine such important economic-management parameters as hourly productivity and operational qualitative features able to ensure the perfect gathering and cleaning of grain for a real contribution to bringing in a physically intact product with higher quality and hygienic safeguards.
An important opening provided by electronics and sensor developments for the management of harvesters has certainly helped facilitate the drive towards this goal and these applications have also led to important technical-agronomic improvements in harvesting operations, including the management of crop residues and soil compaction.
Productivity and quality objectives
Sensor technology has taken on an increasingly important role in the management of operations in the sector of harvesters by enabling manual control as well as running in fully automatic mode applied to the main work parameters from time to time, beginning with the first cutting phase and on to cleaning and loading of the product. The application of sensors, especially for the most critical points of function requiring frequent regulation in relation to harvesting conditions and the product, thus allows the operator to avoid compromising hourly productivity while maintaining threshing up to a high quality standard.
As opposed to a few years ago, it is already possible to quickly regulate the cutting head and every single functional component directly from the drivers cab as well as automatically set the speed of reel rotation and the speed of the harvester's advance. Auxiliary drive sensors using DGPS (Differential Global Positioning System) signals or optical electronic sensors located on the sides of the header itself are of great importance for ensuring the flow of the product across the entire work width while facilitating a more precise registration of the harvesting parameters.
There have been recent developments involving also the feeding channel. In fact the introduction of sensors for maintaining continuous control of the incoming feed flow of the product provides self-regulation of the speed of advance in relation to the load present to thereby optimize the threshing quality and reduce the risk of clogging. Recently brought in for systems with traditional threshing is a system which automatically varies the speed of the straw walker on the basis of the slope of the land. When the harvester is climbing the speed of the straw walker is decreased to lower the speed of straw arriving to the walker whereas on down slopes the operational speed of the straw walker is increased to avoid possible clogging. The option of automatically regulating the speed of the straw walker to suit various harvesting conditions ensures better separation and boosts hourly productivity.
So it is obvious that the ability to have information which is continuously integrated for monitoring all operational parts which now makes it possible to intervene continuously for the control of each individual component to instantaneously regulate them in relation to real operating conditions will have position repercussions on the performance of the machine. For this reason now coming to the fore are automatic management systems capable of applying continuous self-regulation for effective grain separation, for example, by acting directly on the main parameters which rule the number of drum RPM, the cleaning system, adjusting fan speed and sieve opening according to the real conditions of the product to harvest.
To further these developments there are also systems for evaluating grain separation now getting the close attention of manufacturers. Recent innovations for evaluating the quality of separation and determining the share of cracked grains call for the use of color cameras located at the top of the conveyer channel. These cameras take instantaneous high definition shots second after second scanned by dedicated software for calculating the various grain components such as straw, chaff or foreign bodies as well as the proportion of cracked grain. The values interpreted are then visualized on the control terminal in graphics and real images and if the limits of the values set are exceeded the operator is given a visual warning signal.
The management of residues
Harvesting is one of the most important crop operations from an agronomic point of view thanks to the possibility of managing crop residues to coincide with the purposes of the farm. This management of residues has taken on a rule of primary importance in recent years due to the increasing spread of plants for the generation of bioenergy and the growing interest of Italian farming enterprises in adopting newer soil preparation techniques in place of conventional techniques based on plowing and successive soil preparation operations.
The correct application of these simplified techniques however means that all the crop residues left behind by harvesting must be shredded and spread uniformly on the harvester's entire work front for speeding up integration into the soil without negatively influencing successive soil preparation and seeding work. This requirement has driven manufacturers to go to work on systems for the distribution of residues, to the point of achieving direct onboard management of the width of spreading, and on avoiding excessive central distribution with a system for automatically regulating the spreader direction of launch in relation to side winds or sloping terrain encountered. This latter solution is made possible by two electro-mechanical sensors installed on the rear of the harvester for detecting lateral wind speed and sloping ground and compensating the direction of launch by acting on flaps for uniform distribution along the entire working width of the harvester.
Greater attention to crop residues has also led manufacturers to install specific devices directly on the cutting header. Recent innovations involve locating the cutting reels behind the header for the accumulation of the basal layer of crop biomass which actually enhances the performance of the harvester by starting cutting at a greater height than than when cutting with a conventional header.
And finally, other innovations recently developed for handling residues for bioenergy production make it possible while harvesting to chop materials and chaff and lay them in windrows by the use of flaps located under the header to facilitate the successive collection of biomass.
Attention focused on compaction
Compaction was not considered a real problem in the past but in recent years manufacturers have become involved in research on solutions aimed at attenuating the effects of soil compaction which have become much more realistic. Reducing weight, the major factor in the problem of compaction, through modifications does not appear easy to do because very often there is a strict correlation between mass and work capacities so at least from the technical point of view it is more feasible to increase the ground contact surface of the tires by using low pressure and wide tread tires or mounting track on the machine. As it is, systems controlled directly from the cab for the automatic control of tire pressure for those mounted on both the front and rear axles are becoming increasingly widespread. In substance, the purpose of these systems is to provide optimum management of the tire parameters according to the conditions the harvester is operating in; the reduction of pressure in the field increases their contact surfaces whereas increased pressure is called for during transport for decreasing resistance to the surface the tires are running on thus reducing wear and consumption and improving driving stability.