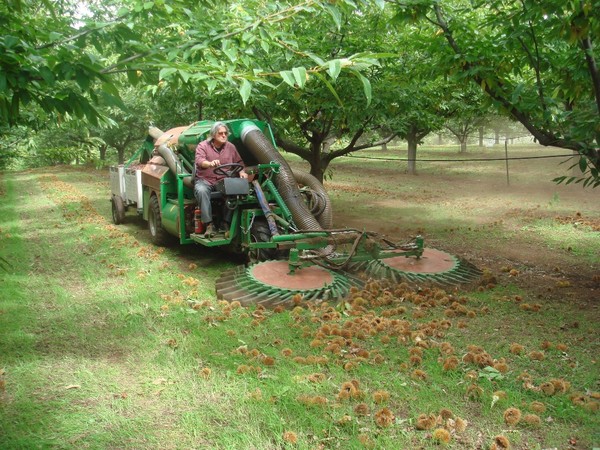
Chestnut cultivation, a challenge for mechanization
Among productive activities in mountainous areas, chestnut cultivation is one which can, in perspective, provide the most interesting returns. The role of mechanization is fundamental and there are now top-level technologies for various phases of work. In the near future, new machines will help to make chestnut cultivations increasingly more efficient and profitable
Chestnut cultivation is one of the activities which can be successful for the economy of mountainous areas though, over the years, the land area allocated for chestnut growing in Italy has declined to the present 780,000 hectares. The reduction of interest in managing chestnut cultivations almost everywhere in Italy is generally assigned to falling earnings linked to commercialization which has given scant value to the product in the recent past. Among the factors which has caused this decline in interest in chestnut crops, especially for the new generation, is undoubtedly the scarcity of innovation for agricultural work in the mountains as well as the slow development of mechanization processes which have supported the primary sector elsewhere. Machinery and equipment created mainly to respond to the needs of farming the plains and hilly areas are, in fact, not very suited for work in tight spaces on terrain lacking uniformity such as slopes which are often steep in mountainous territory. These lands are not considered sufficiently interesting to justify, until recently, the investments required for the production of adequate machinery.
Most recently, the unemployment crisis and public initiatives to favor specific crops – such as the Plan for Mountain Agriculture, the Ministry of Agricultural, Food and Forestry Policy (Mipaaf) Plan for the Chestnut Sector and EU Rural Development Programs (RDP) 2014-2020 – have restored interest in chestnut crops and related mechanization. Many operators still harvest the nuts manually but the manufacturing industries, which have not stopped innovating, are attracting the interest of these growers in the areas of greatest importance for chestnut cultivation.
Harvesting machines put to use can simultaneously reduce the time and cost of this operation while ensuring an increase in the quality of the product and allowing more timely work. The Semek 1000 trailed nut harvester from Facma, located near Viterbo, picks up nuts from the ground mechanically and has been shown to produce good results on level land. Other models feature a suction pick-up which allows them to work on terraced slopes and travel on the roads running through the plantation. This is a case of partial mechanization because the one or two flexible suction pipes are held by walking workers who maneuver them but these operations considerably increase yield over that achieved by manual harvesting. On trial are present are various machines of this type, self-propelled or mounted on a tractor three-point hitch, and under study are models which are adaptable for reversible cultivators. Facma’s C 380S is a a self-propelled aspiration harvester with an hydraulic transmission and powered by a Diesel 4T VM D754 TE3 rated at 83 kW. This machine, which can be run by a single operator, can also be equipped with the RM2010 mechanical pick-up and under study are improvement in maneuverability for avoiding abrasions and micro-lesions on the husk of the fruit. The real cost of mechanical harvesting will depend on the cost of these machines when they reach the market and the way they are used. The deployment of counter-rotating brushes to form tiers of heaped nuts which are then suctioned up can be used only on level ground and the search is on to lessen costs, which are still high, for the machine in relation to the surface area. Often in use in rugged mountainous areas are backpack suction machine such as those turned out by Cifarelli in Voghera, near Padua. There are also the turbo pick-up types like those by Tonutti in Remanzacco, near Udine, for more extended areas. Aspiration harvesters with good power make it possible to pick up the husk and fruit with light weight suction tubes at distances of up to 20 m from the machine.
The product is then sent through a valve to a conveyor inside the machine. The yield depends on the quantity of the product which has been accumulated on the ground. Excellent trailed and self-propelled turbo pick-up harvesters are manufactured in Italy with power between 30 kW to 60 kW and beyond, as needed. At most, two workers are required on the worksite and the yields are high, up to 800 kg/hr if the product is abundant and located on level ground. Tonutti, Facma, Chianchia and De Cloet are manufacturers in this sector. Also the University of Turin is at work on these issues and has created a prototype capable of harvesting some 160 kg/hr with waste at 8% on dry ground conditions on sloping terrain. This machine is driven by a 13 kW motor and is equipped with a brush with perpendicular operation to create a tier which can be harvested ahead of the machine and behind making it safer for work on strongly sloping terrain. The Plan for the Chestnut Sector calls for mechanization management models which are suitable for the various growing systems and especially aimed at providing the operator with information for rationalizing choice and the best use of the machine in relation to specific conditions. Also the new Rural Development Programs envision new measures for mountainous areas and forestry which the regions can enact under regulation 1305/2013 to foster the use of machines for chestnut cultivations.