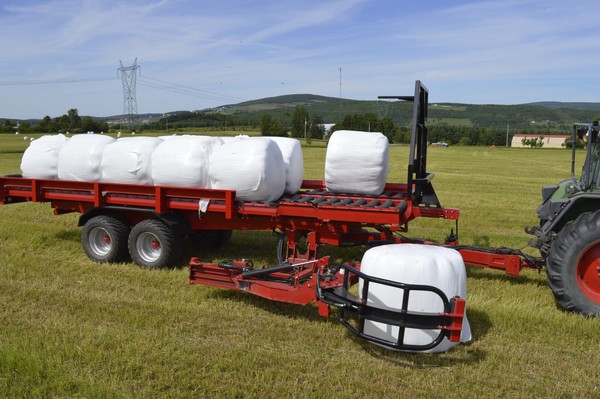
High automation for bale wagons
Whether equipped with devices to catch and load or used only for transport, bale-loading wagons have become very popular especially among contractors as a valuable aid to minimize the time required to deliver loads of forage and straw to their customers
The baling of hay and straw and, more recently, the wrapping of semi-hazed fodder to create mini-silos has led to the spread of so-called "bale-loading wagons," i.e., trailers exclusively designed to intercept, load, place on board, transport, and unload bales.
This equipment is especially appreciated by contractors, who often have to make long transfers on roads open to traffic in order to serve their customers. Therefore, in order to ensure adequate profitability of their activities, they must have highly automated machines capable of performing the entire working routine with just one tractor and, of course, just one operator.
The bale load capacity of bale loaders is usually affected by bale shape, size (and density), which, as we know, can vary quite widely, depending on the internal volume of the baler's pressing chamber.
With a standard width of 120 cm, bales diameters usually range from 120 to 180 cm, while for large prismatic (or parallelepiped) bales, the variability is even greater, primarily in terms of length. A rather common "format" is 240x70x120 cm (WxHxD), but bigger big balers can pack 300x90x120 cm bales.
The mass of the bales depends on the size and the degree of drying of the forage and the density achieved by baling. As a rule, the higher the density, the better, since less air (i.e., less oxygen) is trapped inside the material, to the benefit of product shelf life. The dry matter content (which is what matters in the end) is generally up to 180 kg/m³ for wrapped bales of hay and up to 210 kg/m³ for large prismatic bales. Ultimately, both bales and large parallelepiped bales can reach a mass of several hundred kilograms.
If the large prismatic bales are laid down in the field following an obligatory geometry, i.e., with one of the two widest sides of the parallelepiped resting on the ground, the question arises for round bales of how they come to be loaded. Usually, flat plots of land are placed on their outer circumference but on surfaces with a particular slope, and even if they are sometimes wrapped, they are placed on the ground on one of the two flat sides. Moreover, particularly if the pick-up for transfer to the farm occurs sometime after baling, the bales can be concentrated at the edge of the field, thus making further processing possible on the entire cultivated area. These various product arrangements involve different ways of intercepting and loading the bales.
Furthermore, the bales can be stored on trailers either vertically, i.e., with the flat sides touching the bed, or horizontally, i.e., side by side and stacked one on top of the other along their outer circumference. This has led to the development of various kinematic handling solutions, all of which are usually hydraulically driven, given the size of the loads to be handled.
The machine structure
The basic frame of the bale-loading wagons is the classic agricultural trailer. Depending on the permissible load, it is equipped with a different number of axles with a possible pivoting support wheel used for field operations. In fact, the market offers single-axle wagons, both traditional and "bilico" types, with single or double (or even triple) axles, close together. A considerable number of two-axle models are also available (also in this case possibly double close together) placed symmetrically in respect to the platform. For this specific type, a further significant variation in the main elements of bale loaders involves mounting the front fifth wheel. The device allows the entire front axle to be steered to benefit the machine's maneuverability, particularly in tight spaces. On the negative side, compared to wagons with fixed drawbars, the execution of some operations (especially reverse turns) is not the easiest, and a certain degree of familiarity is required in managing the tractor-operator combination.
Furthermore, the option of closely spaced axles (and possibly of twin tires, sometimes with a wide section and low inflation pressure) has several advantages. It makes it possible to mount wheels with reduced diameter, and therefore to keep the platform low, and ultimately also the maximum height of the load, so as to have a center of gravity as close as possible to the ground (and therefore more excellent stability), and to be able to travel on the road without problems even under low bridges. Moreover, the twinning of the wheels makes it possible to provide wagons with capacities suitable for transporting a considerable number of round bales to benefit the efficiency of the operation. Finally, using wide, low-pressure tires (so-called "floating" tires, often offered as an option to traditional tires) ensures reduced compaction of agricultural land and an increasingly appreciated aspect in terms of sustainability, even in haymaking.
If licensed for use on public roads, bale-loading wagons, similarly to all trailers of the same type, must be equipped with all the standard equipment, i.e., drawbar with the approved eye, hydraulic and pneumatic brakes, lighting kit, etc. More specifically, to make typical field operations possible, some models are equipped with an offset drawbar so that the bale can be intercepted and loaded laterally to the tractor's path. The drawbar must then be locked in line with the tractor during road transport for clear safety reasons.
Bale handling
Leaving aside the models used only for transport, i.e., made up of flatbed and bale containment structures (which must therefore be loaded with a tractor equipped with forks or clamps), models equipped with dedicated loading (and unloading) devices involve operating methods that are sometimes very different from each other, especially concerning transport efficiency, particularly as regards load stability, above all for cylindrical bales. As a matter of fact, if, on the one hand, the bale placement on the flat side is more steady, on the other hand, the bale placement with a base on the outer circumference seems easier to manage.
However, the developed mechanisms involve picking up the bales from the ground, lifting (with possible rotation of the bales, sometimes in pairs), placing them on the pallet and/or on overlapping rows, and finally moving them for final positioning. In some cases, the function of ground discharge is also envisaged, usually at the rear but sometimes also at the side.
There are many practical implementations, but the devices are still operated by hydraulic cylinders, obviously managed directly from the driver's seat, sometimes even by remote control units as an alternative. The solutions for interception are particularly interesting. The use of slides, grippers, levers, and half cages, which in some cases constitute the final element of more complex mechanisms capable of rotating and moving the bale at the same time. In all cases, it should be emphasized the considerable robustness of the whole, given that it is a matter of handling material with a mass of several hundred kilograms.
Intercepting and loading
Generally speaking, there are two solutions for catching the bale. In the first, the bale is loaded in line with the wagon on the short side, so the latter must necessarily be equipped with an offset drawbar since it advances on a trajectory parallel to that of the tractor pulling it. As an alternative, it is the wagon that is in line with the tractor, therefore loading is carried out with a mechanism that takes the bale from the side and then moves it (sometimes rotating it) onto the bed.
On some models, the ultimate versatility in bale interception (in whatever position it is lying in the field) is represented by a rotating and translating gripper employing slides, guides, and articulated arms, which can therefore grasp the bale wherever it is and place it on the wagon in the desired position.
Some manufacturers have developed original mechanisms to load several elements in a single solution if the bales are lined up in a single row. Basically, two cylindrical half-cages placed on the two sides of a double overlapping platform rotate outwards by 180° until they reach the ground. Then, the tractor's advancement engages each of the two half-cages with 4-5 bales which, when fully loaded, perform the opposite movement for loading onto the upper platform. The latter is lifted (again hydraulically) to make room for the bales loaded on the lower platform by repeating the routine described above. This allows up to 20 bales to be stored on the wagon so that the maximum capacity of the equipment can be adequately exploited to the benefit of transport efficiency. If the bale lies on the ground on one of the two flat sides, in some cases, the front 3-point hitch of the tractor is fitted with an attachment that gently tilts the bale without damaging it, even if it is wrapped in plastic film.
Storage onboard
In order to find a suitable position on the wagon that can optimize the available volume (and capacity) and at the same time ensure a sufficient level of safety during transport, the bales must be handled in different ways. They can be moved along the flatbed using carpets of chains and sleepers (and sometimes assisted in their movement by bulkheads moved by hydraulic cylinders) or on a series of rollers placed in parallel rows or stacked with articulated mechanical arms, or rotated thanks to special half cages. A rather common solution is the one illustrated above, i.e., bales are moved linearly along the long side of the trailer bed using a moving carpet. This option also helps with subsequent unloading in the final storage area, i.e., in barns or under canopies.
The attachments
Since bale-loading wagons are essentially manufactured on a similar basis to trailers, they can benefit from trailers' many of the options offered today. For example, the steerable axle (to improve maneuverability in tight spaces, particularly for models with a large load volume and capacity), various types of hydraulic or pneumatic braking systems, large-section and low-compaction tires, a tipping platform, etc.
There are also many specific attachments, however. Among these, considerable help is provided by the many solutions that make it easier to manage the various phases of the routines that form the entire operation. The aim, of course, is to be able to employ only one operator, who constantly remains in the tractor's driving seat. To this end, flexible cable controls, hand control, or even radio controls are available.
The options that can be mounted on the rear part of the wagon are also interesting, with a hydraulically operated cantilevered half-moon sideboard available to increase loading capacity and a rear platform (also hydraulic) for unloading bales directly.